Infrared Thermal Imagers Are The Guardians Of Power Equipment
Infrared thermal imagers use non-contact temperature measurement technology to quickly identify abnormal hot spots in power equipment and prevent faults. Its full-field scanning capability significantly improves detection efficiency and has played an important role in the maintenance of key equipment such as transformers and switchgear, helping the safe and stable operation of power systems.
The safe and stable operation of power equipment is an important basis for ensuring the normal production and life. In the power system, key equipment such as transformers, switchgear, and transmission lines are under high load for a long time, which is prone to failures or even accidents due to overheating. As a non-contact temperature measurement tool, infrared thermal imagers can quickly detect abnormal hot spots in equipment and become an indispensable technical means for the maintenance of power equipment.
Working principle of infrared thermal imagers
Infrared thermal imagers receive infrared radiation emitted from the surface of an object and convert it into a visual temperature distribution image. Different temperature areas are displayed in different colors on the image, allowing operators to intuitively identify abnormal hot spots. Compared with traditional spot thermometers, infrared thermal imagers have full-field temperature measurement capabilities and can scan a large range of equipment at one time, significantly improving detection efficiency.
OnikaOptics (Wuhan) Co., Ltd. was established in 2017. Onika Optics relies on its own infrared chip technology. Its products achieve a balance between high-precision temperature measurement and rapid response in the power field, and can adapt to the needs of complex environments such as substations and distribution rooms.
Typical application scenarios in power equipment testing
(1) Transformer testing: Parts such as transformer oil pillows and bushing joints are prone to local overheating due to poor contact or insulation aging. Infrared thermal imagers can scan at long distances under power conditions, avoiding the safety risks of traditional detection methods.
(2) High-voltage switch cabinet monitoring: Infrared imaging can detect hidden overheating at the contacts and busbar connections in the cabinet to prevent arc short-circuit accidents.
(3) Transmission line inspection: Using drones equipped with thermal imagers can efficiently complete defect screening of overhead line insulators, hardware and other components.
In actual operation, inspectors need to pay attention to influencing factors such as ambient temperature and wind speed, and compare and analyze historical equipment data to avoid misjudgment. Through algorithm optimization, Oonica Optics' products can automatically compensate for environmental interference and improve the reliability of outdoor detection.
Technical advantages and economic benefits
The application of infrared thermal imaging technology brings multiple values to the power system:
(1) Preventive maintenance: detect potential defects in advance and avoid losses caused by sudden downtime. According to statistics, timely handling of an overheated joint can prevent repair costs of about tens of thousands of RMB.
(2) Extend equipment life: through temperature trend analysis, reasonably arrange maintenance cycles and reduce mechanical damage caused by excessive disassembly.
(3) Improve safety: non-contact detection method keeps workers away from high-voltage dangerous areas and reduces operational risks.
Based on more than 20 years of infrared application experience, Oonica Optics' solutions have been verified in many substations and power plants in China. The cost advantage brought by the localization of its core components enables small and medium-sized power companies to afford the purchase of related equipment.
Precautions for use and development trends
To ensure the effectiveness of detection, the following points should be noted:
(1) Select a suitable thermal imager resolution. The recommended pixel for general power detection is not less than 320×240.
(2) Avoid periods of direct strong light during testing to avoid reflection interference.
(3) Establish equipment temperature files and formulate differentiated warning thresholds.
In the future, with the development of artificial intelligence technology, infrared thermal imagers will gradually realize automatic defect recognition and fault prediction. Some companies have begun to try to connect thermal imaging data to the power Internet of Things platform to build a more intelligent operation and maintenance system. Companies such as Oonica Optics continue to optimize chip performance, and future products still have room for improvement in temperature measurement accuracy and environmental adaptability.
As the "guardian" of power equipment, infrared thermal imagers provide reliable protection for the safe operation of power systems through all-weather, non-destructive monitoring methods. The continuous advancement of technology will promote its greater role in emerging fields such as new energy power stations and smart grids.
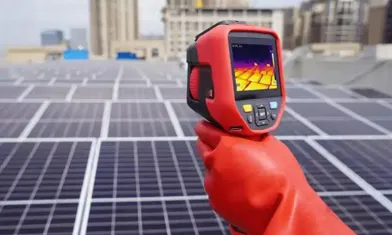
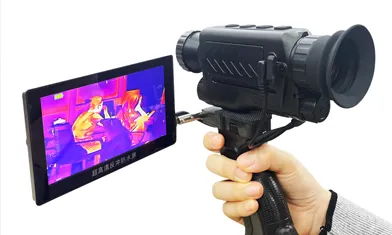
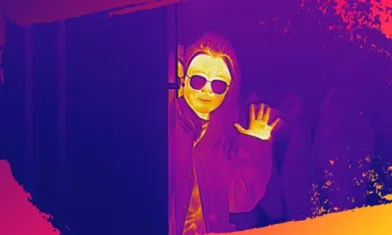
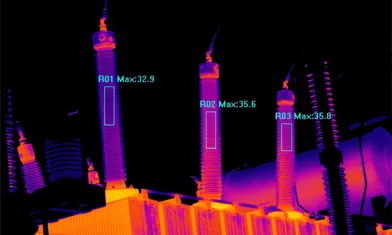